3D printing
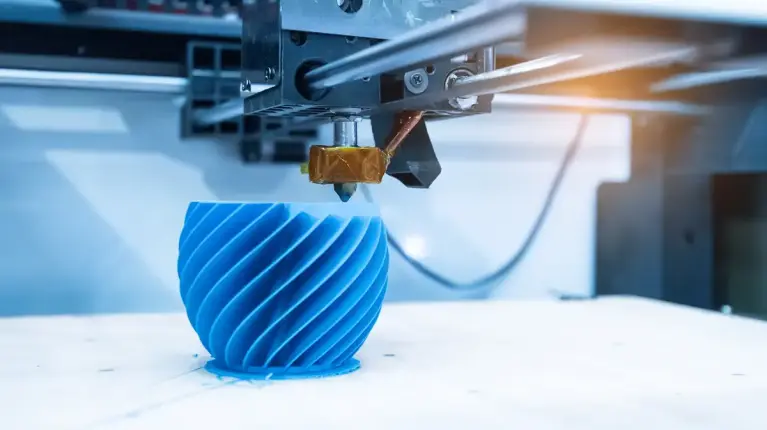
In case of electron beam melting, vacuum is required. Electron Beam Melting is an additive manufacturing method with which it is possible to print material out of titanium, cobalt, chrome alloy, steel, aluminum and copper.
This is mandatory for special parts in the aerospace industry or medical market. Examples for printed parts are turbine plates or hip prosthesis.
Learn more about 3D printing
How does 3D printing work?
The Electron Beam Melting system consists mainly of an electron beam column and a formation chamber. In the electron beam column a high power electron beam is generated which is selectively melting the metal powder in the formation chamber.
After each layer the system is driving down and a new layer of metal powder is added on top. This process continues until the printing of the part is finished.
What are the best vacuum solutions for 3D printing?
Pfeiffer offers a comprehensive portfolio for Electron Beam Melting with vacuum pumps for evacuation, pressure gauges and calibration vacuum pump units, customized vacuum chambers, as well as leak detectors for the localization of leaks.
What vacuum conditions are required for 3D printing processes?
The vacuum in the Electron Beam Melting system fulfills several purposes. On the one side it is protective against oxidation and air bubbles. On the other hand it is required to generate the electron beam in the electron beam column and for focusing the beam.
The vacuum is avoiding a collision of the electrons with other gas particles which would cause a deflection of the beam. Due to this a high mean free path is required and therefore a low end pressure. Typical final pressures are in the range of 5x10-5 hPa (mbar). A fast pump down time is required to minimize the time needed for a part change.
Within the process, gases like helium will be injected to ensure a clean and controlled environment. The typical process pressure is therefore in the range of 10x-3 hPa (mbar). The vacuum equipment must be insensitive against dust and particles and should have a good resistance to heat.