Vacuum and Leak Detection in the Medical Industry
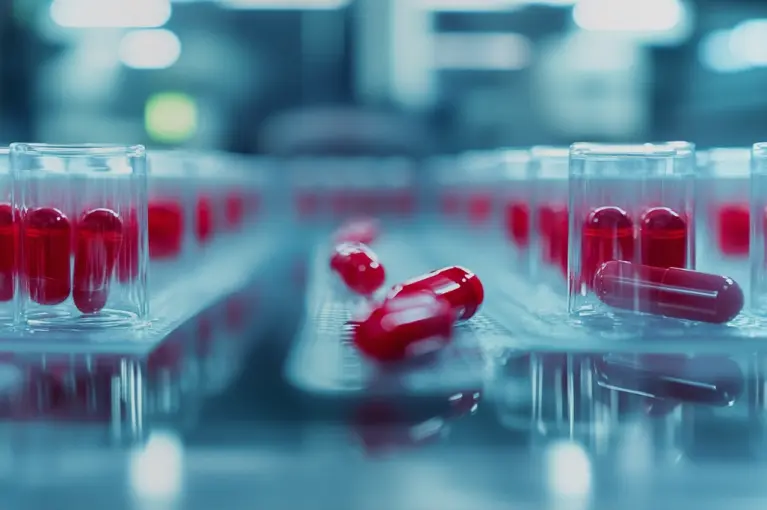
In the medical field, the well-being of people is paramount. Safety, precision, and reliability are crucial in protecting lives. Vacuum and leak detection technologies are essential for vital applications such as sterilization, medical devices, diagnostic imaging, container closure integrity testing (CCIT), residual gas analysis (RGA), and medical accelerators.
Pfeiffer has decades of experience supporting medical manufacturers and research institutions worldwide. Our deep understanding of sensitive, human-centered medical applications enables us to deliver tailored vacuum and leak detection solutions – ensuring patient safety, regulatory compliance, and trust in every step of medical innovation.