Fields of application
Thin film deposition in solar cell manufacturing
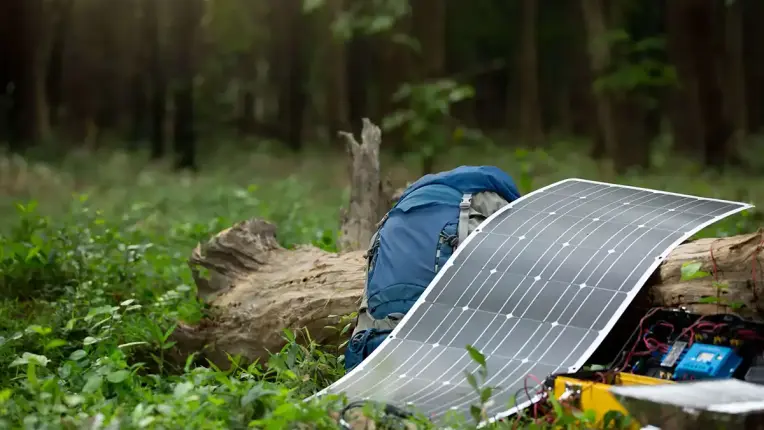
Application requirements for thin film deposition in solar cell manufacturing are long service intervals and high uptime, carbon-free vacuum, simplest on-site maintenance, and high suction speed with fast pump-down.
How does thin film deposition in solar cell manufacturing work?
There are various types of solar cell technologies - one of the major technologies is based on thin film deposition. The main advantage of this technology is the low material consumption within the solar cell production.
Beside materials like Cadmium Telluride (CdTe), Copper-Indium-Gallium-Selenide (CIGS) will be often used for the absorber layers. These layers can be deposited on inflexible substrates like glass or on flexible substrates like metal band or foil or on flexible thin glass and then the substrate is inserted into a big vacuum chamber.
In this chamber several PVD processes like sputtering or evaporation take place to generate a multilayered solar cell. To deposit these layers, a vacuum in the range of 10-3 to 10-6 hPa (mbar) is needed depending on the process. Due to the large surfaces, a high suction speed is inevitable.
This vacuum needs to be clean and carbon free to ensure high quality layers.
What are the best vacuum solutions for solar cell manufacturing?
Pfeiffer has a complete product portfolio for your system along with a team of experts to find the right solution for your application. We offer dry and oil lubricated vacuum pumps and pumping systems with high suction speeds.
With our hybrid or magnetic levitated turbopumps we ensure a low base pressure. To guarantee process stability and safety, our pressure gauges and leak detectors are the right choice.
Crystalline silicon cells
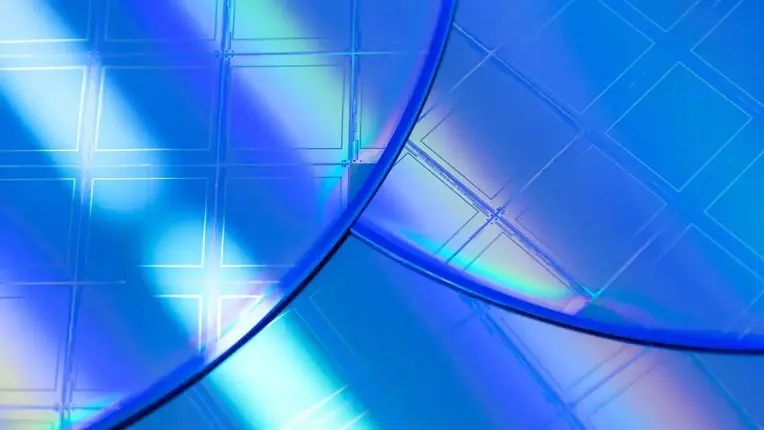
Application requirements for crystalline silicon cells include long service intervals and high uptime, carbon-free vacuum, simple on-site maintenance, and high suction speed with fast vacuum pump-downs.
How do crystalline silicon cell technology work?
There are various types of solar cell technologies - the major technology is based on crystalline silicon wafers. These solar cells demonstrate the highest efficiency of all technologies. The major layers are based on silicon nitrid but being compiled with different functional layers to further optimize the cell efficiency.
Current trend in this market is the optimization of the reflection layers on the rear side of the cell to increase the absorption inside the cell (Passivated Emitter Rear Contact - PERC). A PERC layer is created through an additional film deposition by using either PECVD or ALD process.
New technologies like heterojunction solar cells are combining advantages of several solar technologies like the decreased material consumption of thin film deposition, with the high efficiency of crystalline silicon cells. The solar wafers are inserted into a vacuum chamber, whereby several PVD and PECVD processes take place to generate a multilayered solar cell.
To deposit these layers, a vacuum in the range of 10-3 to 10-5 hPa (mbar) is needed depending on the process. Due to the large surfaces, a high suction speed is inevitable. This vacuum needs to be clean and carbon free to ensure high quality layers.
What are the best vacuum solutions for crystalline silicon cell manufacturing?
Pfeiffer has a complete product portfolio for your system along with a team of experts to find the right solution for your application.
We offer dry and oil lubricated vacuum pumps and pumping systems with high suction speeds. With our hybrid or magnetic levitated turbopumps we ensure a low base pressure.
To guarantee process stability and safety, our pressure gauges and leak detectors are the right choice.