Fields of application
PECVD, SACVD
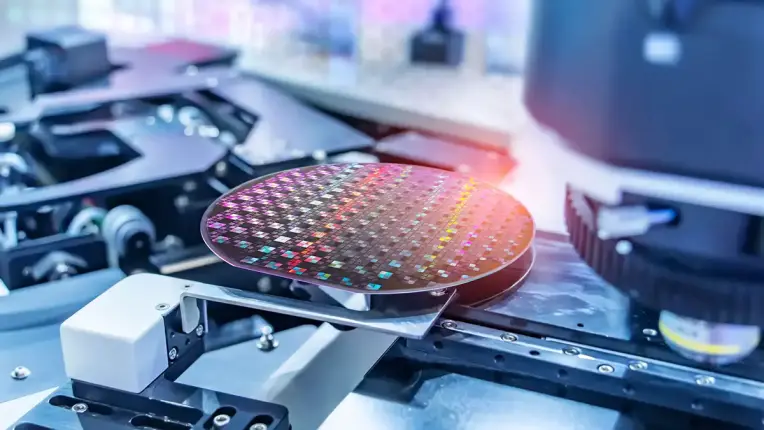
How does PECVD, SACVD work?
PECVD process allows to reduce substrate temperature which is critical to the device, whereas SACVD at high temperature and high pressure is used for high deposition rates. Featuring better step coverage than PVD technology, PECVD and SACVD are mainly used to deposit the critical insulating dielectric layers that isolate and protect the electrical structure, such as silicon oxides, silicon nitrides and low-K.
What vacuum conditions are required for PECVD and SACVD processes?
Except High Density Plasma deposition (HDPCVD), most of processes operate under primary vacuum, in the mbar pressure range. As the chemical reaction occurs in the chamber, precursors react to form by-products which are evacuated by vacuum pumps.
Such by-products are commonly a great challenge for the dry pumps as their nature may vary depending on the type of precursors which are used: Highly corrosive, condensable, or solid, some applications combining even all of these simultaneously.
What are the best vacuum solutions for PECVD, SACVD?
Pfeiffer provides a full range of dry pumps designed to handle these challenges: Sophisticated thermal management prevents deposition, advanced materials reduce corrosion rate and multi-stage Roots design manages powder evacuation.
Physical Vapor Deposition (PVD)
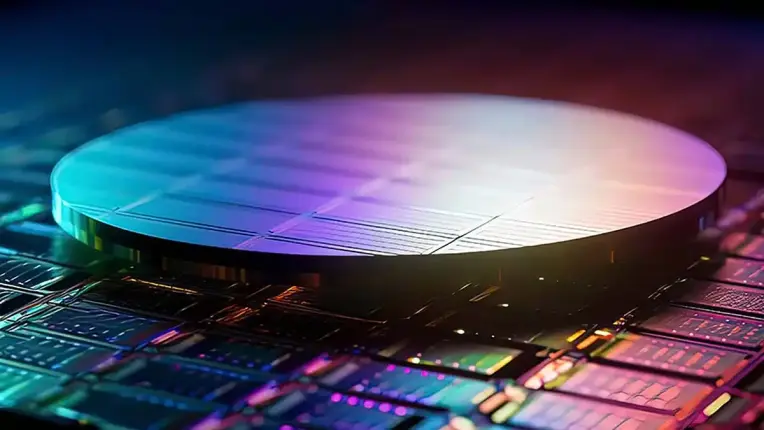
How does PVD work?
The most common PVD process used is sputtering technology: The target material is bombarded by the inert gas (mostly argon) ions generated in the plasma. Then the target material is ejected from the surface and deposits on substrate.
What vacuum conditions are required for PVD processes?
Such process operates at high vacuum below 10-3 to 10-7 Torr range, requiring the use of dry roughing pumps, turbopumps as well as cryo pumps. As there is no chemical reaction, this process generates no by-products and is therefore a clean application for vacuum pumps.
What are the best vacuum solutions for PVD?
Pfeiffer supplies the A4H series, a full range of dry pumps and magnetically levitated turbopumps dedicated to PVD applications. Our ATH-M turbopumps are qualified on many PVD tools at major OEMs.
Atomic Layer Deposition (ALD)
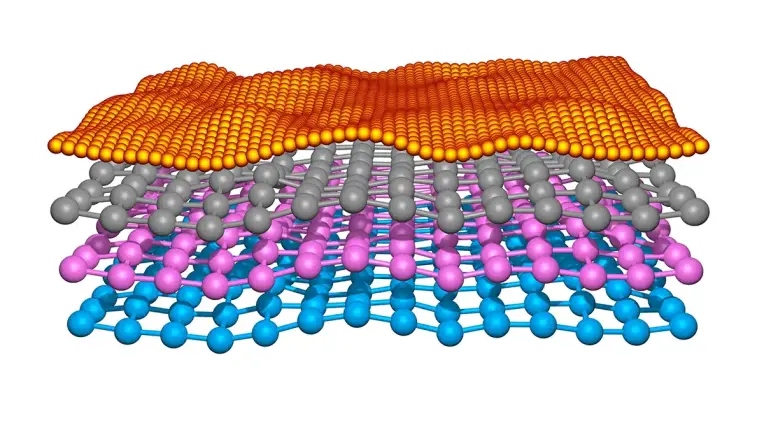
This technology is used to deposit a variety of oxides, nitrides or metals, enabling manufacturing of the most advanced devices including 3D architectures where thickness conformity and uniformity are crucial.
How does ALD work?
ALD deposition cycle consists of sequential injections of precursor and reactant in the reactor. Chemical reaction energy is activated either by temperature (Thermal ALD) or by plasma (PE ALD). In between each pulse, N2 purge is injected to evacuate by-products formed by precursor adsorption on the surface and unreacted precursor and reactant.
As the reaction is self-limited by nature, film thickness is only dependent on the number of deposition cycles performed, allowing a control of the deposited layer at the atomic scale. ALD process can be performed on single wafer or batch equipment, each of them featuring specific advantages.
What vacuum conditions are required for ALD processes?
Most of ALD processes operate under primary vacuum, in the 10-1 to 5 mbar pressure range. On high volume manufacturing equipment, high pumping capacity in the range of 1,800 to 4,500 m3/h is required for fast evacuation of precursors during purge steps, insuring high throughput.
On smaller R&D equipment, smaller dry pumps can be used, between 600 to 1,200 m3/h. Generated by-products are commonly a great challenge for the dry pumps as their nature may vary depending on the type of precursors which are used: Highly corrosive, condensable, or solid, and some applications combining all these simultaneously.
Diffusion, LPCVD
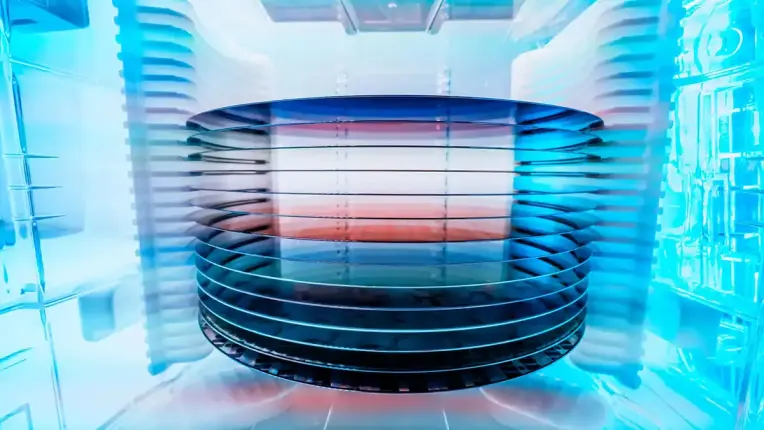
Diffusion is a thermal process used for oxidation and nitration of the wafer surface, or to change the electrical properties of the doped layers.
How does Diffusion, LPCVD work?
Both LPCVD & Diffusion technologies use thermal energy to activate the chemical reaction, typically in the range of 500 to 900 °C. Besides excellent step coverage & high purity deposition, this technology allows a much larger substrate surface treatment than other CVD technologies. LPCVD or Diffusion equipment are commonly batch types, processing up to 200 wafers simultaneously.
What vacuum conditions are required for Diffusion, LPCVD processes?
Depending on the material to be deposited, several precursors can be used leading to multiple varieties of by-products to be handled by dry vacuum pumps: Condensable or solid, some applications combining both simultaneously.
Molecular beam epitaxy (MBE)
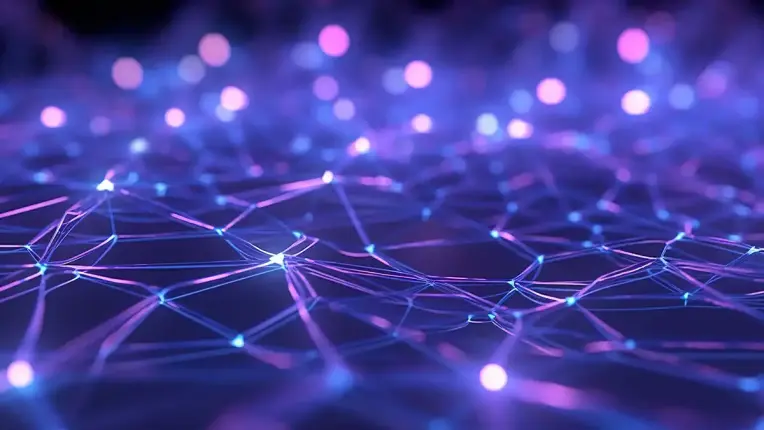
Nowadays, MBE is widely used for the production of semiconductor devices. It is also one of the most important techniques for Nano- and Quantum technologies.
How do MBE work?
In solid source MBE, ultra-pure elements such as gallium and arsenic are thermally evaporated in vacuum (from 10-8 hPa (mbar) to 2x10-5 hPa (mbar) typical). The atomic fluxes from the cells reach the wafer where the epitaxial growth can happen. In the example of gallium and arsenic, single-crystal gallium arsenide is formed. The atoms impinging on the surface adsorb, migrate and incorporate into crystalline lattice of the wafer. They also can desorb if the substrate temperature is too high.
Controlling the temperature of the source will control the rate of material impinging on the substrate. The substrate temperature affects the migration length and desorption rate. The term "beam" means that evaporated atoms do not interact with each other or residual gases until they reach the wafer, due to the long mean free paths of the atoms at low pressure. Therefore, simple mechanical shutters can be used to abort the flux.
-
Molecular beam epitaxy system by Innolume GmbH
Why is a vacuum necessary in MBE?
Vacuum is essential in Molecular Beam Epitaxy (MBE) to ensure high purity of grown films by minimizing contamination from residual gases. The ultra-high vacuum environment allows precise control of atomic fluxes from evaporation sources to the substrate, facilitating high-quality epitaxial growth. It also prevents contamination from external sources, crucial for semiconductor devices and Nano-Quantum technologies.
The vacuum helps control substrate temperature, affecting the migration length and desorption rate of atoms, which is vital for achieving the desired crystalline structure. MBE takes place in high vacuum or ultra-high vacuum (10-8 – 10-12 hPa (mbar)) with a typical deposition rate of 1,000 nm per hour, requiring better vacuum conditions to maintain low impurity levels.
The absence of carrier gases and the ultra-high vacuum environment achieve the highest purity of grown films. Pfeiffer offers various vacuum pumps, gauges, and mass spectrometers designed for MBE applications to ensure ideal vacuum conditions and high-quality epitaxial growth.
What are the best vacuum solutions for MBE?
Pfeiffer provides different dry rough pumps and turbopumps with high compressions ratios. For MBE applications, Pfeiffer also can provide vacuum gauges to control the pressure in the system and mass spectrometers to perform the residual gas analysis (RGA).