Fields of application
Dielectric etch
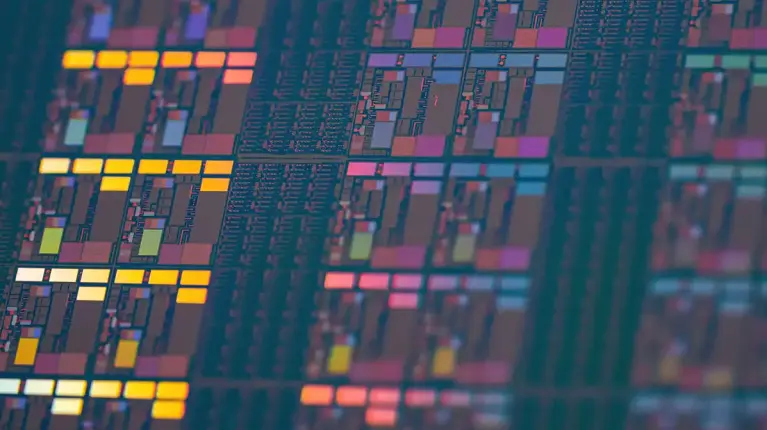
As critical dimensions are continuously shrinking, high uniformity and selectivity are needed to meet required electrical performance on such tiny structures: this is achieved by plasma or reactive ions etching process.
How does dielectric etch work?
Etching gas, commonly fluorine based, are injected in the reactor. Plasma generates radicals which react on the wafer surface by creating a volatile by-product. Thanks to device patterning obtained by lithography and through control of plasma reaction and temperature, the material is selectively etched from the surface at the desired rate.
What vacuum conditions are required for dielectric etch processes?
Dry dielectric etch processes operate at low pressure, in the range of 10-2 to 10-3 hPa (mbar).
In order to maintain a low vacuum, turbopumps are mounted directly on the chamber reactor, backed by primary dry pumps installed in the basement. As gas flows are continuously increasing, required turbopumps pumping capacity vary from 1,600 to 4,000 l/sec on the newest generation reactors. Dry pumps typically require pumping speeds from 600 to 1,200 m3/h.
By-products to be evacuated are condensable, high temperature operation is therefore critical for extended lifetime.
What are the best vacuum solutions for dielectric etch?
Pfeiffer provides a full range of turbopumps and primary dry pumps designed to handle these challenges. Our magnetically levitated turbopumps ATH-M series provide vibration free high vacuum and high temperature / high flow operation. ATH-M series are qualified at the major OEMs on the most advanced dielectric etch chambers.
Our A4H dry pumps feature sophisticated thermal management to prevent deposition, for long lifetime & low operating costs.
Conductor and polysilicon etch
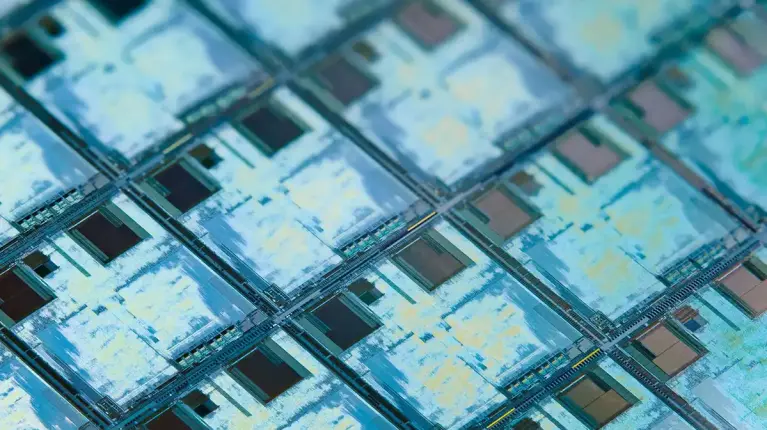
Dry polysilicon (Poly-Si) etch consists of selectively removing polysilicon to create the transistor gate.
As critical dimensions are continuously shrinking, high uniformity and selectivity are needed to meet required electrical performance on such tiny structures: this is achieved by plasma or reactive ions etching process.
How does conductor and polysilicon etch work?
Etching gas, commonly chlorine or fluorine based, are injected in the reactor. Plasma generates radicals which react on the wafer surface by creating a volatile by-product. Thanks to device patterning obtained by lithography and through control of plasma reaction and temperature, the material is selectively etched from the surface at the desired rate.
What vacuum conditions are required for conductor and polysilicon etch processes?
Dry conductor & Poly-Si etch processes operate at low pressure, in the range of 10-2 to 10-3 hPa (mbar). In order to maintain a low vacuum, turbopumps are mounted directly on the chamber reactor, backed by primary dry pumps installed in the basement. As gas flows are continuously increasing, required turbopumps pumping capacity vary from 1,600 to 3,000 l/sec on the newest generation reactors. Dry pumps typically require pumping speeds from 600 to 1,200 m3/h.
By-products to be evacuated are condensable and highly corrosive. This represents a great challenge for vacuum pumps, which should be able to operate at high temperature under a very corrosive environment.
What are the best vacuum solutions for conductor and polysilicon etch?
Pfeiffer provides a full range of turbopumps and primary dry pumps designed to handle these challenges. Our magnetically levitated turbopumps provide vibration free high vacuum and high temperature / high flow operation.
Featuring optional corrosion resistance, our ATH-M series are qualified at major OEMs on the most advanced conductor & Poly-Si etch chambers.
Our A4XN dry pumps feature advance materials to withstand corrosion & sophisticated thermal management to prevent deposition, for long lifetime & low operating costs.
Dry stripping and cleaning
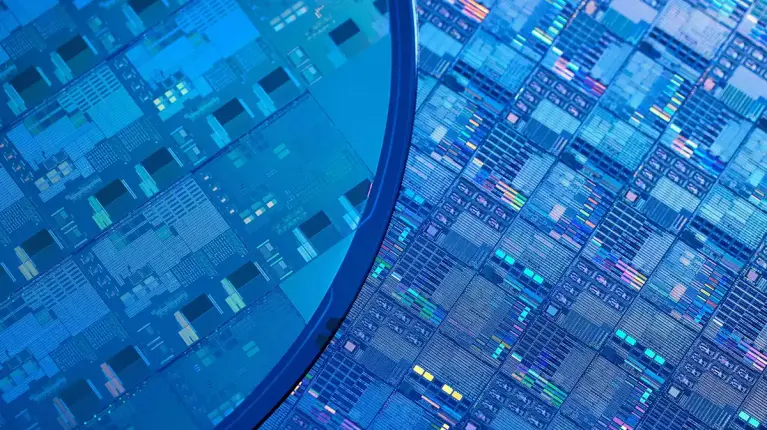
Most common stripping application consists of removal of photoresist, either through wet process or dry plasma process under vacuum (also named ashing).
Other cleaning processes (commonly named descum) consist of removing polymer residues in device trench after etch process.
How does dry stripping and cleaning work?
Using a plasma source, reactive species are generated, commonly oxygen or fluorine. For advance nodes manufacturing, trend is to replace oxygen by hydrogen to reduce wafer surface oxidation. As the plasma is formed, many free radicals are created which could damage the wafer. In order to reduce wafer damage, most stripping equipment use a remote or downstream plasma configuration. Reactive species combine with the photoresist to form volatile byproduct which is evacuated by a vacuum pump.
What vacuum conditions are required for dry stripping and cleaning processes?
Dry ashing or stripping process operates at a working pressure in the range of 1 hPa (mbar) and typically requires dry pumps with pumping speeds in the range of 600 to 1,800 m3/h, with emerging needs up to 3,000 m3/h. As some equipment are not equipped with load lock chambers, fast pump down times are required for high throughput.
What are the best vacuum solutions for dry stripping and cleaning?
Byproducts, consisting mainly of carbon oxides and polymers, are not critical for vacuum pumps. Our A4H dry pumps are well adapted to this application, featuring long lifetimes & low operating costs.
Atomic Layer Etch (ALE)
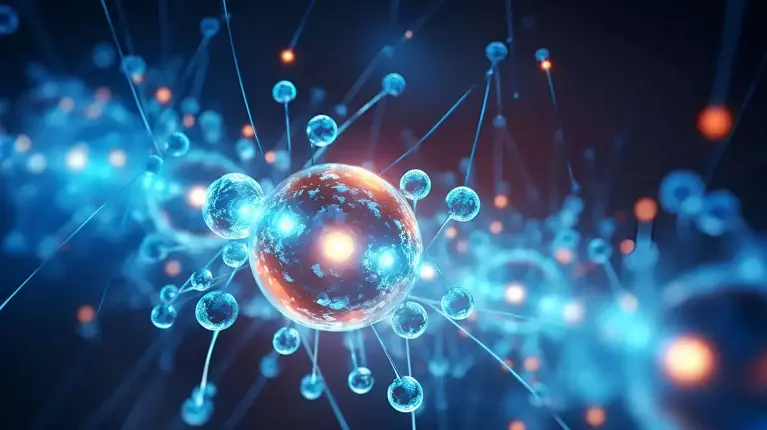
This technology is used to selectively etch a variety of oxides or Poly-Silicon, enabling manufacturing of the most advanced devices where high selectivity, high uniformity and low damage are crucial, as a counterpart of the ALD technology.
How does ALE work?
As for ALD, ALE process cycle consists of sequential injections of reactive gases and ionized noble gas in the reactor, commonly energized by plasma.
In between each pulse, N2 purge is injected to evacuate reactant and by-products formed by precursor adsorption on the surface. As the reaction is self-limited by nature, etch thickness is only dependent on the number of cycles performed, allowing a control of the etched layer at the atomic scale. ALE process is generally performed on single wafer equipment.
What vacuum conditions are required for ALE processes?
As for conventional plasma etch process, chlorine and fluorine based chemistries are used, depending on the material to be etched. New emerging ALE processes can also include some deposition steps for improved control of etch profile. This new trend involves the use of silicon precursors typically present on ALD or CVD applications.
ALE processes operate at low pressure, in the range of 10-2 to 10-3 hPa (mbar). In order to maintain a low vacuum, turbopumps are mounted directly on the chamber reactor, backed by primary dry pumps installed in the basement. As gas flows are continuously increasing, required turbopumps pumping capacity vary from 1,600 to 4,000 l/sec on the newest generation reactors. Dry pumps typically require pumping speeds from 600 to 1,200 m3/h.
By-products to be evacuated are condensable and highly corrosive. This represents a great challenge for vacuum pumps, which should be able to operate at high temperature under a very corrosive environment.
What are the best vacuum solutions for ALE?
Pfeiffer provides a full range of turbopumps and primary dry pumps designed to handle these challenges. Our magnetically levitated turbopumps provide vibration free high vacuum and high temperature / high flow operation. Featuring optional corrosion resistance, our ATH-M series are fully compatible with the most advanced ALE processes.
Our A4XN dry pumps feature advance materials to stand corrosion & sophisticated thermal management to prevent deposition, for long lifetime & low operating costs.