Fields of application
Architectural glass coatings
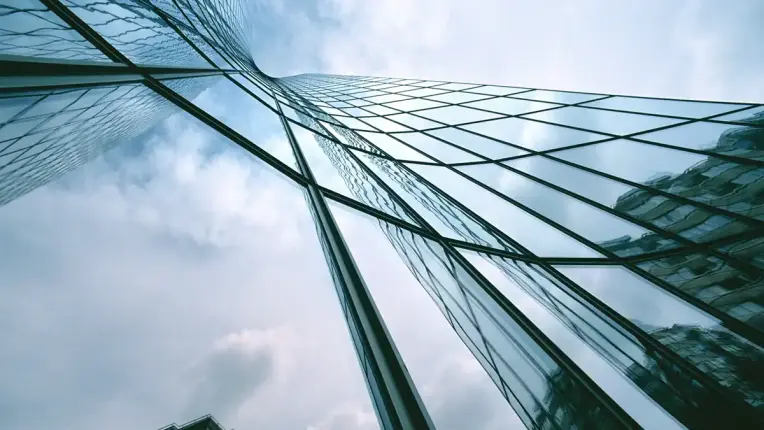
For thin film coating applications, key requirements include long maintenance intervals for maximum uptime, a carbon-free vacuum environment, and the simplest on-site maintenance. Pumps with high compression ratios, fast pump-down times, and high suction speeds are essential to ensure efficient, reliable performance and high-quality coatings.
How do architectural glass coatings work?
The glazing material is transported into a large coating chamber via a roll band. Inside this chamber a sputtering process takes place. For this a plasma is generated under vacuum conditions of 1x10-3 to 1x10-5 hPa.
A carbon free vacuum is essential for the process and surface quality. Typically high suction speed is needed due to the large surface of architectural glass.
What are the best vacuum solutions for architectual glass coatings?
Pfeiffer product line covers all application specific needs. We offer dry and oil lubricated vacuum pumps and vacuum pump units with high suction speeds.
To reach a lower vacuum pressure we offer turbopumps with hybrid and magnetic levitation. To ensure a stable and safe process we also offer pressure gauges and leak detectors.
Optical coatings
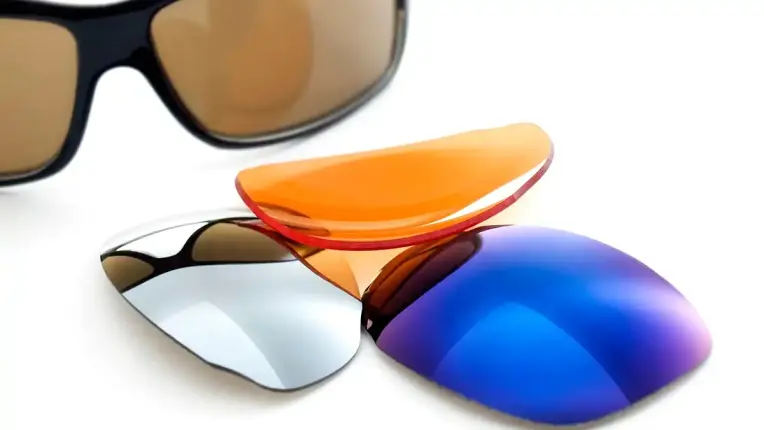
Application requirements for optical coating include a clean, carbon-free vacuum, long maintenance intervals for maximum uptime, low operating costs, and the simplest on-site maintenance to ensure efficient, reliable performance and cost-effective operation.
How do optical coatings work?
The part to be coated is inserted into the coating chamber in which a sputtering process takes place. In this chamber a plasma is generated under vacuum and the thin film is coated onto the part.
Typical vacuum ranges are between 1x10-3 to 1x10-4 hPa. One major requirement is to have a carbon free vacuum in order to enable a high quality coating process.
What are the best vacuum solutions for optical coatings?
Pfeiffer has been present in the optical coating market with his innovative products since the beginning of this development and offers you the right solution for your application. For the vacuum generation we offer single pumps such as rotary vane pumps, screw pump as well as complete vacuum pump units.
To reach a lower pressure turbopumps are used either with hybrid levitation or magnetic levitation. Furthermore we offer pressure gauges and leak detectors to guarantee process stability.
Wear protection coatings
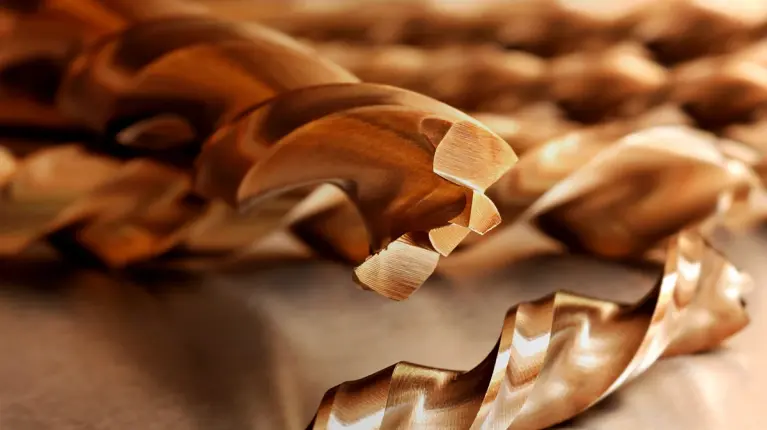
Wear protection coatings require a vacuum system with low base pressure, fast start-up times, and high suction speed to ensure efficient coating processes. Additionally, systems should have low maintenance intervals, dust resistance, and a low cost of ownership to maintain long-term performance and cost-effectiveness.
How do wear protection coatings work?
There are basically two different methods of wear protection, chemical vapor deposition (CVD) and physical vapor deposition (PVD). The material to be deposited, also called a target, is usually in solid form and is vaporized in a coating chamber by arc discharge under vacuum.
Typical working pressures are in the range of 1x10-1 hPa - 1x10-4 hPa. Layers of the vapor deposition can be found in many areas of industry and other branches.
What are the best vacuum solutions for wear protection coatings?
With our technical expertise and complete line of products for wear protective coatings, we are ready to assist single rotary vane and screw pumps.
To reach lower pressure level we also offer turbopumps suitable for dusty applications. To monitor your process we can provide pressure gauges and leak detectors.
Decorative coatings
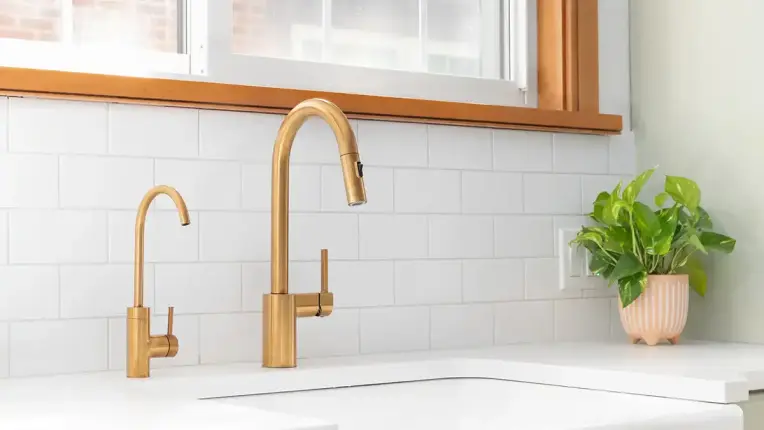
Decorative coatings require a carbon-free vacuum environment, long maintenance intervals, and maximum uptime to ensure consistent quality. Additionally, systems should have low operating costs and the simplest on-site maintenance to optimize efficiency and reduce overall operational expenses.
How do decorative coatings work?
The part to be coated is inserted into a chamber and coated with either a PVD or CVD process. The process itself is a sputtering process in which a plasma is generated under vacuum which enables the deposition on the part.
The vacuum inside the chamber is typically in a range between 10-3 to 10-4 hPa. A carbon free vacuum is essential to guarantee a high quality surface.
What are the best vacuum solutions for decorative coatings?
Pfeiffer supplies this application since the beginning with the right product portfolio and expertise. For the vacuum generation we offer dry and oil lubricated vacuum pumps as well as complete vacuum pump units.
To reach a lower pressure, we offer hybrid and magnetic levitated turbopumps. We also offer leak detectors and pressure gauges to ensure process stability and safety.