- Real-time measurement
- High sensitivity
- Multiple detection technologies
- In-line monitoring
- Airborne Molecular Contamination (AMC) sampling
- Environmental monitoring
- Contamination prevention
- SEMI S2/S8 compliant
- Auto-calibration function
- Flexible delivery options for FOUPs
- Optimization of queue times
Contamination Management Systems
Improving the yield in the semiconductor industry
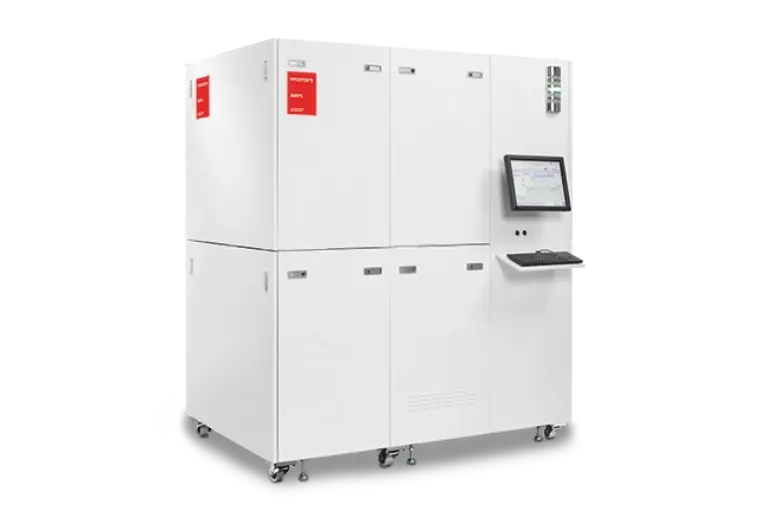
Solutions for contamination management from Pfeiffer Vacuum+Fab Solutions improve the yield in the individual process steps of sensitive devices production.
APA 302
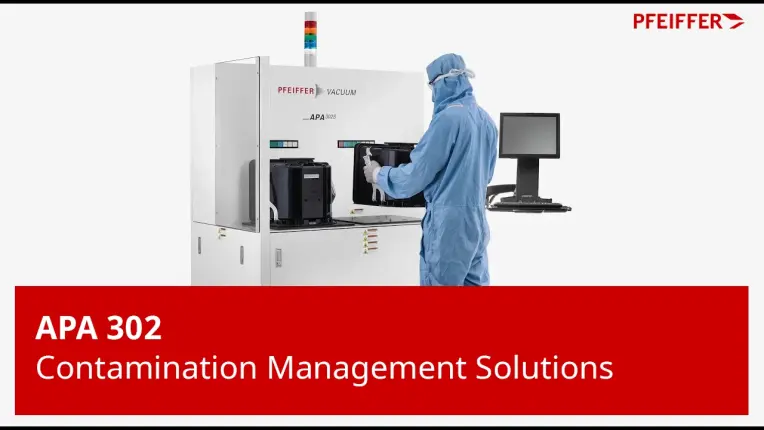
Benefits of the APA 302
Efficient contamination monitoring
The APA 302 is a unique in-line monitoring tool for advanced chip manufacturing in clean room environments. This innovative equipment measures airborne molecular contamination (AMC) in a FOUP and the surrounding environment in real-time with high sensitivity in the ppbv-range. Moisture and AMC, such as hydrogen fluoride (HF), are released in the FOUPs slot-to-slot space during queue times, which can generate crystal growth on patterned wafers, leading to yield loss and performance degradation. The APA 302 by Pfeiffer samples the AMC through the FOUP filters. The measurement occurs in two minutes with a high sensitivity in the ppb-range through ion mobility spectroscopy, flame ionization detection, Fluorescence UV or cavity ring-down spectroscopy. When there is no FOUP on the load ports, the APA 302 monitors the surrounding clean room environment.
Reliable analysis of the FOUP environment
To guarantee performance, the SEMI S2/S8 compliant APA 302 is equipped with an auto-calibration function activated at regular intervals. The monitoring of AMC within the APA can be performed in PODs with or without wafers. FOUPs can be delivered either manually or through overhead hoist transportation (OHT) on the two load ports. This allows the queue times between individual process steps to be optimized, increased values of contamination to be immediately recognized, and yields to be increased.
ADPC 302
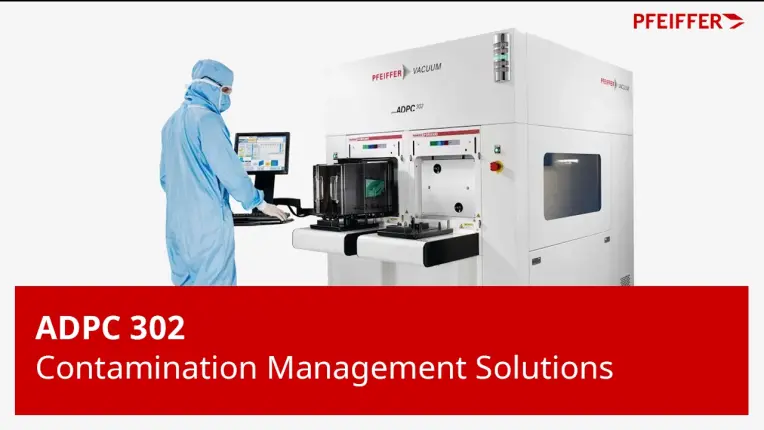
Benefits of the ADPC 302
Efficient particle monitoring
Submicrometer particles can cause defects that may lead to considerable yield loss. Even the smallest particles measuring 0.1 µm can damage the structure of semiconductor chips. The innovative ADPC 302 measures the number of particles in wafer transport carriers, the Front Opening Unified Pods (FOUP) and Front Opening Shipping Boxes (FOSB). The fully- automated patented process localizes and counts particles from the carrier surfaces, including the door. Qualified by leading fabs, this system can be used for both serial manufacturing and R&D analysis. The main applications include carrier characterization, cleaning strategy optimization, and cleaning quality checks.
Advantages of the dry process
The dry process (Dry Particle Counter) of the ADPC 302 shows clear benefits compared to the traditional wet method (Liquid Particle Counter). The main advantage of the dry process is that the particle measurement is fully-automatic. It is integrated into the production process and does not require time outside the manufacturing period. Thanks to the fully-automatic measurement, the process does not require an additional operator. The test time is only seven minutes, making the ADPC 302 four times as fast as traditional systems. It is possible to test eight transport boxes in one hour.
APR 4300
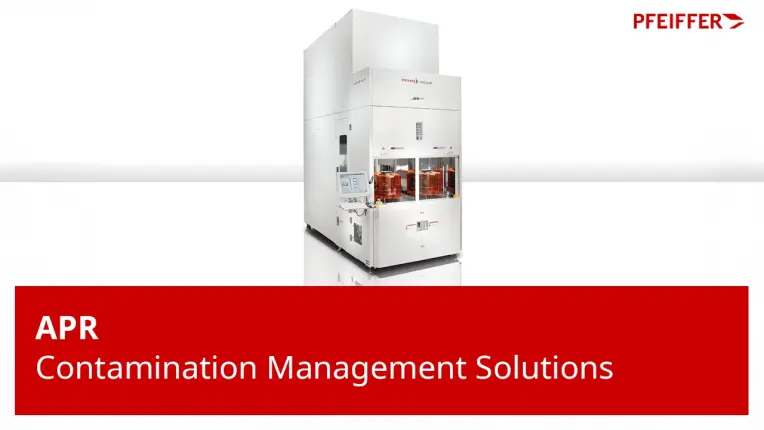
Benefits of the APR 4300
Reliable decontamination and protection
The APR is a system designed for the decontamination of wafers and the protection during queue time. Airborne Molecular Contamination (in short AMC) lowers the yield and quality in semiconductor manufacturing. The APR effectively prevents the adsorption of contaminated organic or inorganic molecules on the surface of wafers and transport boxes. By evacuating chambers in the APR, the probability of adsorption is significantly reduced. In this way, the yield of a fab can be significantly increased and the queue times between the individual process steps be optimized.
AMPC
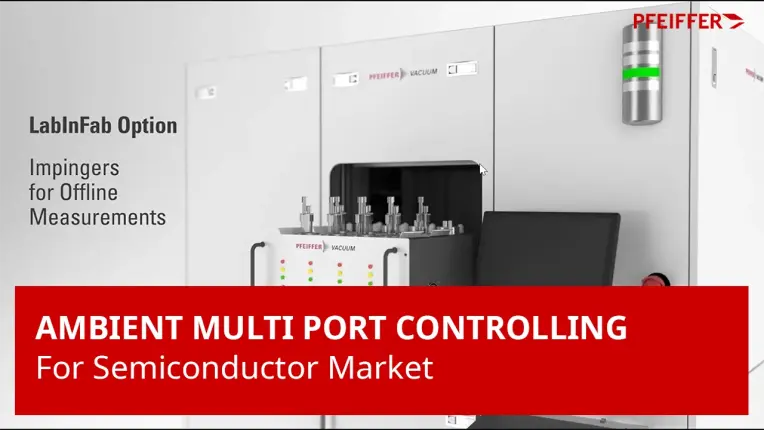
Benefits of the AMPC
Data management and fab communication
Airborne molecular contamination (AMC) in IC fabs is a major factor in yield loss. To control and understand the sources of contamination, Pfeiffer offers a unique solution for monitoring clean rooms and Equipment Front End Modules (EFEM) in the semiconductor market. The AMPC gathers the most advanced analyzers to detect and quantify acids, bases and organic compounds in up to 96 locations within a fab, thanks to an innovative and integrated valve design. AMPC range includes two tools: AMPC S and AMPC L with different external dimensions, number of lines, and options. Additionally, the AMPC Extension Frame provides 39 U of space for extra analyzers, which can be used for upgrades of existing AMPC units or added to new AMPC S and AMPC L units. The tool software allows the end users to set various alarms when contamination levels exceed defined thresholds. All measurement data and tool parameters are stored in a database that can be transmitted to fabs’ communication protocols, providing customers with a real-time picture of the fab’s contamination levels. Customers can also remotely access the tool to modify parameters if necessary.
Customer Benefits
- Real-time compound measurement (acids, bases, organic compounds)
- Innovative software to manage sampling lines priority, quality check (QC) and alarms
- 96 sampling lines gathered onto one tool (up to eight analyzers)
- High throughput (analyzing and cleaning within three minutes)
- No cross-contamination from one sampling line to another
FAQ
How does contamination occur?
In the semiconductor industry, wafers emit reaction by-products during transport and waiting times. Moisture and airborne molecular contaminants (AMC), such as hydrogen fluoride (HF), react in the tight spaces of transport boxes (pod systems) with oxidants from the ambient air (H₂O and O₂). These reactions trigger undesired crystal growth on structured wafers, leading to a decline in quality and decreased manufacturing yield.
In pharmaceutical industry, contamination such as humidity, oxygen or microbiological ingress can impact drug stability throughout the product lifecycle.
What makes Pfeiffer's contamination systems special?
Pfeiffer's many years of experience as a provider of vacuum technology have shaped our know-how and understanding of the processes, equipment and environment of production systems. Based on this knowledge, we have developed advanced contamination management solutions specifically for the semiconductor and pharmaceutical industries. These solutions identify and minimize contamination, thereby increasing yield at each step of the process.
To guarantee quality and a high yield in manufacturing, knowledge about contaminants in the packaging of devices and their immediate environment is crucial.
In semiconductor industry, continuous analysis within the process cycle is possible with the APA 302. The fully automated process of the ADPC 302 localizes and counts particles on the inner surfaces of transportation carriers. The APR 4300 even goes a step further.
The AMPC is the ideal solution for clean room and equipment front end modules monitoring (EFEM).