- Tailored for die casting units with a clamping force greater than 750 metric tons
- Recipient concept designed to meet the requirements of large die casting units
- Achieves and sustains the desired pressure in the mold cavity quickly and reliably during the first stage
- Prevents air inclusions
- Enables trouble-free, cost-effective operation due to low maintenance costs
- Reduces rejects thanks to reliable process control and high reproducibility
Multi-Stage Vacuum Process
Reliable and efficient solutions for die casting
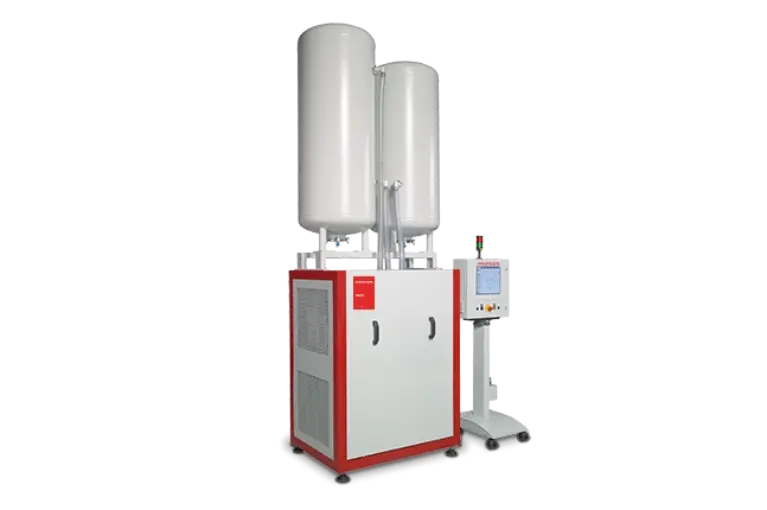
The purpose of vacuum in a die casting system is to evacuate a given volume of air from the mold cavity and the shot sleeve as rapidly as possible, preventing air inclusions in the castings.
Vacu²
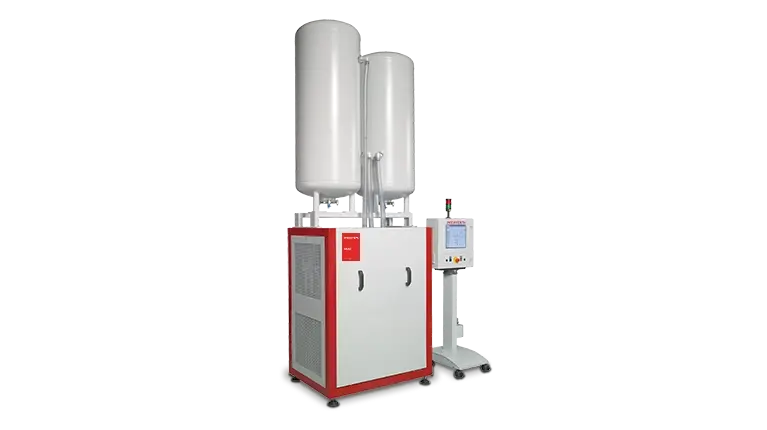
Vacu² Eco
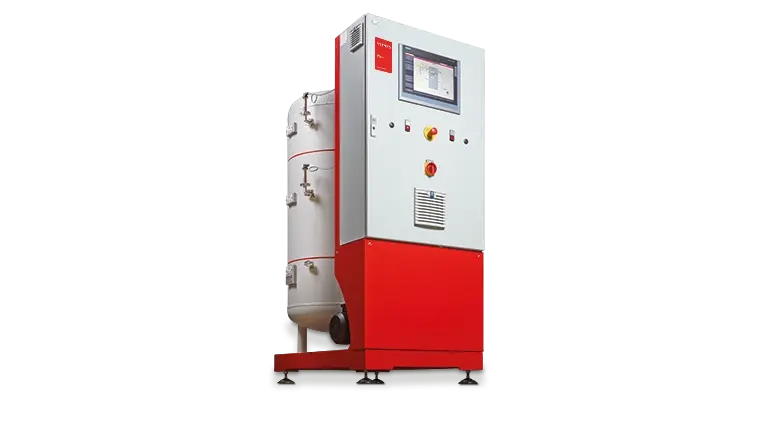
- Tailored for die casting units with a clamping force of less than 750 metric tons
- Highly economical with great efficiency in suction volume and low energy consumption
- Recipient concept ideally matches small chamber and mold volumes
- Equipped with high-resolution 15-inch touchscreen display, fully integrated in a compact control cabinet
- Optimized duct volume to evacuate small-volume molds
- Service-friendly system design and high manufacturing control through proven and reliable technology
- Offers optimal cost-performance ratio
FAQ
How does the multi-stage vacuum process work?
In our multi-stage vacuum process, the shot sleeve and mold cavity are evacuated in two stages. In the first stage, the air is extracted from the shot sleeve via a wide cross-section line to quickly achieve the desired pressure. In the second stage, air is extracted directly from the mold. This two-stage evacuation ensures rapid and efficient air removal, preventing air inclusions in the castings.
How does the control system optimize the process?
The control system processes pressure measurements taken at four different locations at various points of time during the casting process into process-relevant data. This provides precise information about the current status of the system, avoiding unnecessary rejects and significantly reducing costs in die casting processes.