Vacuum Valves
Essential for the design of a vacuum system.
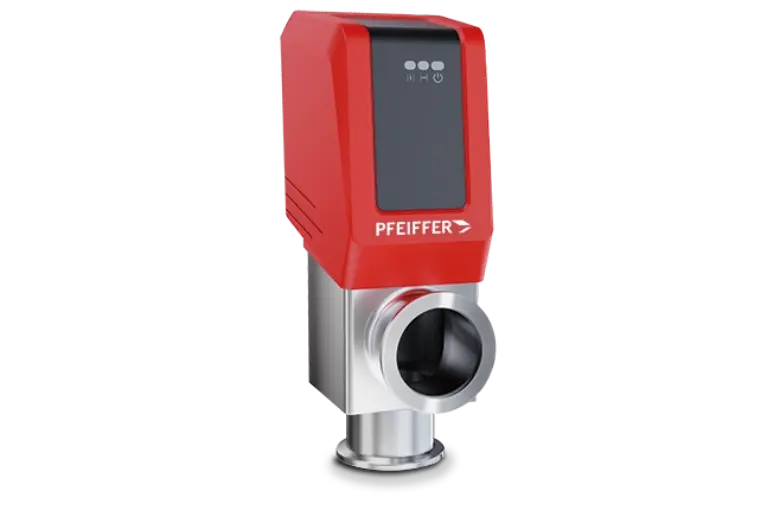
Vacuum valves play a crucial role in the design and functionality of vacuum systems, ensuring precise control and reliability across various industries and research applications.
Our valve portfolio includes a wide range of pressure regulating valves and isolation valves, available with different actuators and flange types to meet diverse operational needs.
Isolation valves
Isolation valves are crucial for maintaining vacuum conditions by isolating sections of a vacuum system. They control gas or liquid flow and can be manually, pneumatically, or electrically operated. Suitable for various applications, including semiconductor manufacturing, R&D, and industrial processes, isolation valves ensure reliable sealing and operational efficiency.Pressure control valves
A pressure control system consists of three essential components: valve, controller, and pressure gauge. The primary function of pressure control valves is to regulate the pressure inside a vacuum chamber and the gas flow within vacuum systems. These valves are ideal for applications demanding precise process control, such as those in the semiconductor and coating industry.Actuators
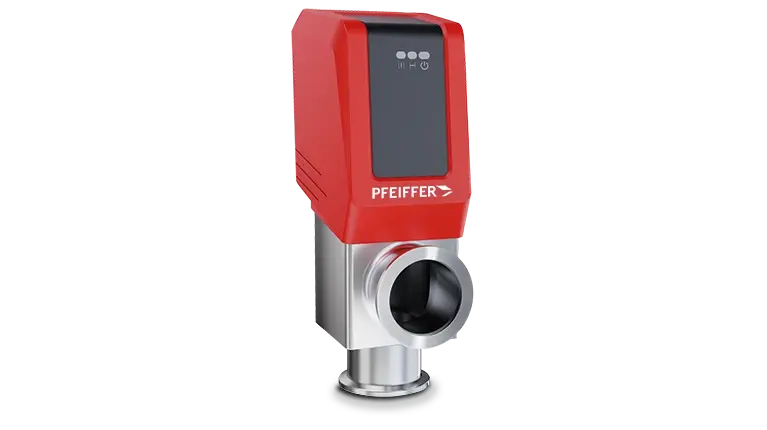
Manual actuation
Manual valves with a handwheel or a quick-closing/quick-opening mechanism are temperature-resistant up to 150 °C and can be operated without restrictions from electronic components.
Electric actuation
Electric actuation utilizes electric motors to convert electrical energy into precise mechanical movement, enabling automated and reliable control without the need for compressed air.
Pneumatic actuation
Pneumatically actuated valves require an oil-free compressed air supply.
Electro-pneumatic actuation
Pneumatically actuated valve with built-in solenoid valve to control the compressed air supply to the valve.
Flanges
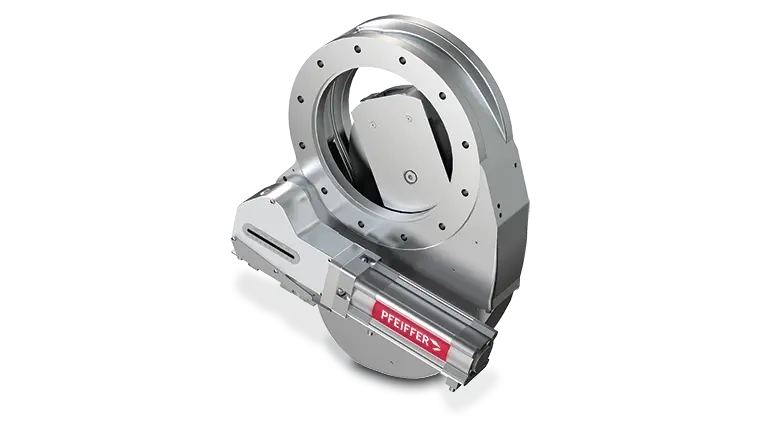
- ISO-KF
- ISO-K
- ISO-F
- CF
- Threads
FAQ
Which vacuum valve suits my application?
Criteria to find a suitable vacuum valve for your application:
- Purpose: The application significantly influences the selection of the valve. Requirements vary depending on whether the valve is primarily used to open and close vacuum lines or to regulate pressure.
- Installation and system compatibility: The physical dimensions of the available installation space and the flanges of the vacuum pump and chamber have a direct influence on the selection of the appropriate valve size.
- Pumped media: The composition of the gases flowing through the valve strongly influences the choice of materials, ensuring durability and reliability of the valve.
- Temperature: Knowledge of the expected temperatures is essential in order to select the appropriate materials for the valve body and seals, guaranteeing long-lasting functionality.
- Pressure: Understanding the pressure conditions the valve will be exposed to influences the valve selection.
How are valves activated?
Pneumatically operated valves utilize compressed air to control valve movement. The required air pressure for actuation typically ranges between 4 and 8 bar.
There are two main types of pneumatically operated valves:
- Single-acting valves (commonly smaller angle valves) use compressed air to open the valve, while a spring returns it to its default position when air supply is lost. Most single-acting valves are normally closed, meaning compressed air opens the valve, and the spring ensures it closes when pressure is removed.
- Double-acting valves (typically larger valves) use compressed air for both opening and closing, providing greater control and reliability in demanding applications.
To regulate compressed air flow, a solenoid is used to direct air to the valve’s air cylinder. Electromagnetic valves come with an integrated solenoid, and most vacuum systems require a 24V DC-powered solenoid for operation.
For monitoring purposes, position indicators are available to determine whether a valve is open or closed. Manual valves typically feature a visual indicator, while pneumatic valves can provide direct feedback to the vacuum system, ensuring precise control and monitoring.
What makes Pfeiffer vacuum valves special?
Our pressure control valves incorporate two key innovations designed for exceptional performance:
- At the core of every controller is our patented motor control technology that enables high-speed operation with extremely fine position resolution.
- Our adaptive pressure control algorithm works in tandem with the motor control to ensure virtually error-free pressure regulation.
Which pressure ranges can the valves be used for?
Vacuum valves are suitable for all vacuum applications, with the choice of valve depending on the sealing technology required for specific pressure levels:
- For high vacuum applications (up to 1×10⁻⁸ hPa (mbar)), Pfeiffer offers a wide range of valves with elastomer seals and ISO-KF/ISO-K flanges, ensuring reliable performance.
- For ultra-high vacuum applications, valves with metal seals in the wetted areas and CF flanges are the best choice. All-metal valves with fully metallic seals are also available.
Which seals and sealing mechanisms are available?
Seals and sealing methods play a decisive role in the selection of the right valve for the vacuum system.
- Elastomer seals provide reliable sealing for high vacuum applications. Their temperature resistance depends on both the elastomer material and actuation type.
- Metal seals do not require elastomers and are therefore ideal for ultra-high vacuum applications. They can withstand temperatures up to 300°C.
What types of high vacuum valves are available?
Angle valves divert the gas flow by 90°, while inline valves, with opposite connecting flanges, allow easy installation in straight pipelines. Both variants usually use a bellows as a seal.
Gate valves and isolation pendulum valves are perfect for confined spaces, and ensure unobstructed gas flow with optically free passage. They are designed for high and ultra-high vacuum and often open at low differential pressures of 30 hPa (mbar). Ideal choice for airlocks or upstream of pumps.
Ball valves can also be used in certain high vacuum applications. Cost-optimized KF designs show leakage rates of 10-6 mbar l/s and are temperature resistant up to 80 °C. Special designs are suitable for the HV range and withstand temperatures up to 150 °C.
The choice of the right valve depends on factors such as the process sequence, the process temperature, the ultimate vacuum and the gas composition. In the following sections, we give you an overview of our valve types, seals, sealing mechanisms and drive types. At Pfeiffer, you will find the right valve solution for your vacuum range.