Product Services
Tailored services for your vacuum pumps and leak detectors.
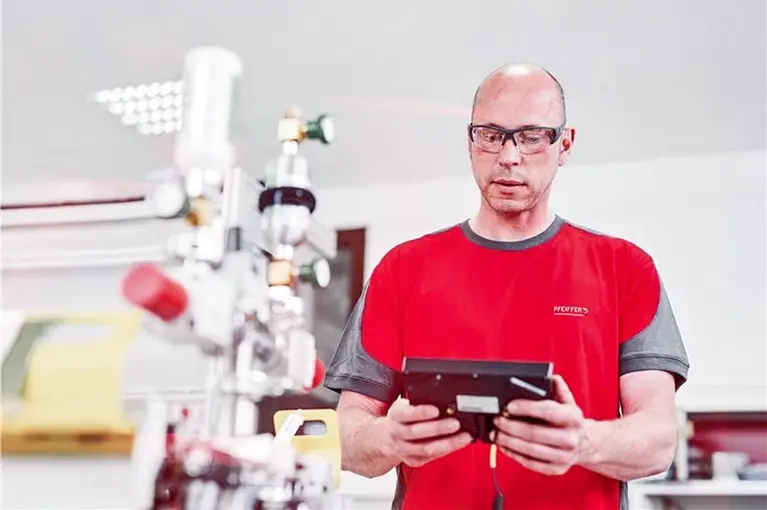
Regular maintenance and servicing are crucial to maximize the availability, performance, and service life of your vacuum equipment. We offer a full range of service solutions to keep your vacuum pumps and leak detectors operating at their best.
Standardized or customized service solutions
Whether you require standardized maintenance or customized service options, Pfeiffer Vacuum+Fab Solutions delivers the right solution across our entire product portfolio.
We offer comprehensive services for all Pfeiffer products. And we are continuously expanding our portfolio with new, product-specific services.
Maintenance
Our product maintenance follows a clear, transparent, and structured approach – typically in up to three consecutive steps.* We aim to keep you fully informed about all recommended and performed work, ensuring your equipment is optimally maintained for maximum performance and longevity.
* Deviations may occur depending on the vacuum pump type.
Repair
At Pfeiffer Vacuum+Fab Solutions, service excellence is consistent across the globe. With more than 50 service locations worldwide, we guarantee first-class support wherever you are. Our repair services include fault analysis, detailed service reports, and the use of genuine Pfeiffer parts and tools – ensuring your equipment is restored to top condition.
Exchange
Our exchange program is a fast, efficient alternative to conventional maintenance or repair. We provide you with a fully overhauled vacuum pump that matches your original product's performance – backed by a full 12-month warranty.1) Your returned pump will be refurbished and added to our exchange pool.
We offer two types of exchanges:
Working exchange2)
Our working exchange is the fastest solution to minimize downtime during maintenance. You receive a comparable fully overhauled product in exchange for your running device that is to be serviced. You then have four weeks to send your faulty pump to us.- Pre-delivery of an overhauled product in exchange for your running unit to be serviced
- Minimization of machine downtime in case of maintenance
- Full 12-month warranty on the exchange product
Standard exchange
Our standard exchange is ideal when your pump is already non-operational. Similarly to the working exchange, you receive a fully refurbished replacement immediately and have four weeks to return your defective device.- Pre-delivery of an overhauled product against your defective device
- Minimization of machine downtime in case of damage
- Full 12-month warranty on the exchange product
2) Available for all vacuum pumps, except diaphragm vacuum pumps.
Product-specific service options
Additional product services
In case of damage
- Repairs and maintenance in our service centers.
- On-site repairs and maintenance by our service technicians.
- Troubleshooting and advice from our technical support team.
Genuine spare parts
- Pfeiffer spare parts and tools are defined during product development to guarantee precise fit and exceptional quality.
- All product improvements are seamlessly integrated into our spare parts.
- After maintenance or repair, your equipment is restored to the latest Pfeiffer technology standards.
Decontamination
- Certified decontamination performed according to the latest industry standards.
- Full compliance with all applicable legal and safety regulations.
- Safe and reliable handling of contaminated material throughout the entire process.
Installation
- Professional support during installation and commissioning.
- Expert instruction provided by our certified service technicians.
- On-site leak detection and gas analysis services.
Telephone support
- Direct remote access to technical product specialists.
- Expert error analysis and troubleshooting.
- Comprehensive application support.
Warranty extension*
- Warranty extension of up to 24 months at a fixed price.
- Full benefits equivalent to the original manufacturer's warranty.
- Complete coverage of parts and labor costs.
Services for turbopumps
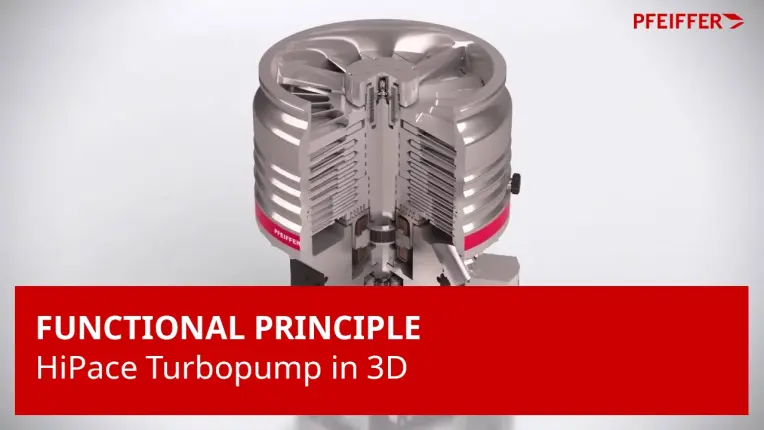
By analyzing data from the installed sensors, any irregularities can be identified during the inspection process.
Maintenance of turbopumps
Inspection | Level 1 | Level 2 | Level 3 |
---|---|---|---|
Annual rotation by operator on site. | Every 4 years by Pfeiffer Service. | Every 4 years by operator on site or Pfeiffer Service. | Every 4-5 years by Pfeiffer Service.1) |
|
|
|
|
Spare parts
| Spare parts
| Spare parts
|
Maintenance level 1
Replacement of operating fluidsOperating fluids in turbopumps must perform a wide range of tasks under challenging conditions to ensure reliable operation. To maintain optimal performance, Pfeiffer offers the replacement of operating fluids as part of service level 1.
Maintenance level 2
Replacement of relevant wear partsDue to their design and usage, wear parts are subjected to significant operational stress. For cost-optimized maintenance, Pfeiffer provides targeted replacement of the wear parts most exposed to wear. During service level 2, the pump is partially disassembled and cleaned. This level also includes all tasks covered in service level 1.
Maintenance level 3
Replacement of all wear partsTo ensure the turbopump continues to meet all operational requirements, service level 3 offers a complete restoration to original technical specifications. At this level, the pump is fully disassembled, thoroughly cleaned, and all wear parts are inspected and replaced. After a final test, the pump is returned with a 12-month Pfeiffer warranty covering all service work performed.
Repair of turbopumps
Minor repair | Rotor-stator replacement |
---|---|
|
|
Turbopump utility film
On our Utility Film Portal,* you will find a range of videos and documents to support the servicing of Pfeiffer products. The portal also offers additional information and tutorial videos covering our pumps and other products.
*Please note: To gain full access to the Utility Film Portal, registration is required.
Services for vacuum boosters
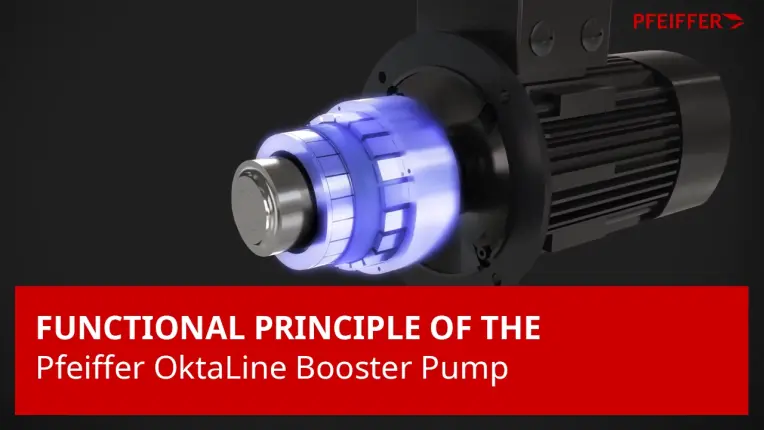
Maintenance of vacuum boosters
Inspection | Level 1 | Level 2 | Level 3 |
---|---|---|---|
Annual rotation by operator on site. | Annually by operator on site. | Every 2 years by operator on site or Pfeiffer Service. | Every 4 years by Pfeiffer Service. |
|
|
|
|
Spare parts
| Spare parts
| Spare parts
|
Maintenance level 1
Replacement of operating fluidsOperating fluids in vacuum boosters must perform a wide range of tasks under challenging conditions to ensure reliable operation. To maintain optimal performance, Pfeiffer offers the replacement of operating fluids as part of service level 1.
Maintenance level 2
Replacement of relevant wear partsDue to their design and usage, wear parts are subjected to significant operational stress. For cost-optimized maintenance, Pfeiffer provides targeted replacement of the wear parts most exposed to wear. During service level 2, the pump is partially disassembled and cleaned. This level also includes all tasks covered in service level 1.
Maintenance level 3
Replacement of all wear partsTo ensure the vacuum booster continues to meet all operational requirements, service level 3 offers a complete restoration to original technical specifications. At this level, the pump is fully disassembled, thoroughly cleaned, and all wear parts are inspected and replaced. After a final test, the vacuum booster is returned with a 12-month Pfeiffer warranty covering all service work performed.
Repair of vacuum boosters
Minor repair |
---|
|
Vacuum booster utility film
On our Utility Film Portal,* you will find a range of videos and documents to support the servicing of Pfeiffer products. The portal also offers additional information and tutorial videos covering our pumps and other products.
*Please note: To gain full access to the Utility Film Portal, registration is required.
Services for rotary vane pumps
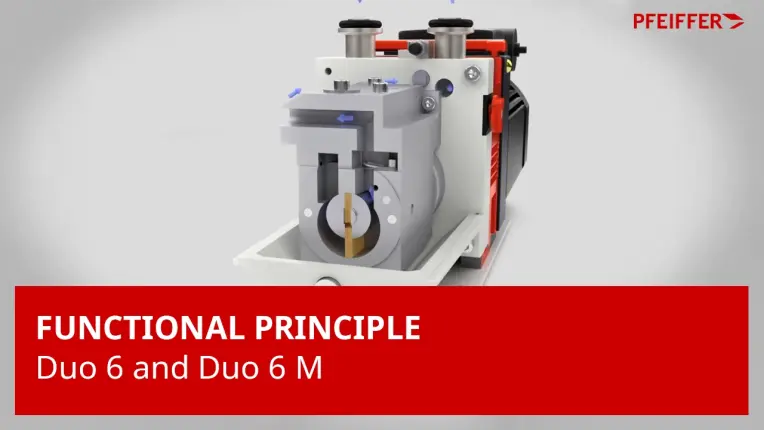
Gate valves, usually made of polymer materials, are also subject to wear and can experience abrasion during operation.
Maintenance of rotary vane pumps
Inspection | Level 1 | Level 2 | Level 3 |
---|---|---|---|
Annual rotation by operator on site. | Annual rotation by operator on site. | Every 2 years by operator on site or Pfeiffer Service. | Every 4 years at Pfeiffer Service Center. |
|
|
|
|
Spare parts
| Spare parts
| Spare parts
|
Maintenance level 1
Replacement of operating fluidsOperating fluids in rotary vane pumps must perform a wide range of tasks under challenging conditions to ensure reliable operation. To maintain optimal performance, Pfeiffer offers the replacement of operating fluids as part of service level 1.
Maintenance level 2
Replacement of relevant wear partsDue to their design and usage, wear parts are subjected to significant operational stress. For cost-optimized maintenance, Pfeiffer provides targeted replacement of the wear parts most exposed to wear. During service level 2, the pump is partially disassembled and cleaned. This level also includes all tasks covered in service level 1.
Maintenance level 3
Replacement of all wear partsTo ensure therotary vane pump continues to meet all operational requirements, service level 3 offers a complete restoration to original technical specifications. At this level, the pump is fully disassembled, thoroughly cleaned, and all wear parts are inspected and replaced. After a final test, the pump is returned with a 12-month Pfeiffer warranty covering all service work performed.
Repair of rotary vane pumps
Minor repair |
---|
|
Rotary vane pumps utility film
On our Utility Film Portal,* you will find a range of videos and documents to support the servicing of Pfeiffer products. The portal also offers additional information and tutorial videos covering our pumps and other products.
*Please note: To gain full access to the Utility Film Portal, registration is required.
Services for scroll pumps
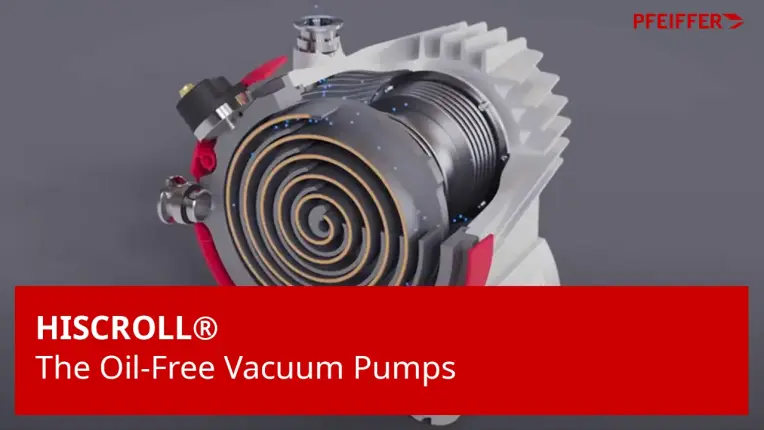
Maintenance of scroll pumps
Inspection | Level 1 | Level 2 | Level 3 |
---|---|---|---|
Annual rotation by operator on site. | Approx. after 2.5 years1) by operator on site. | Optional / if required by operator on site or Pfeiffer Service. | Every 5 years1) by Pfeiffer Service. |
|
|
|
|
Spare parts
| Spare parts
| Spare parts
|
Maintenance level 1
Replacement of the tip sealOver time, individual components of a scroll pump may experience wear due to operational conditions. To maintain optimal performance, the tip seals should be replaced approximately every 2.5 years. Pfeiffer offers the replacement of the tip seals as part of service level 1.
Maintenance level 2
Optional replacement of relevant wear partsIf required, the gas-ballast valve, tip seals and O-rings can be replaced during service level 2. Due to the intelligent design of the pump, service level 2 is easy to perform and can be carried out by the operator on site.
Maintenance level 3
Replacement of all wear partsTo ensure the scroll pump continues to meet all operational requirements, service level 3 offers a complete restoration to original technical specifications. At this level, the pump is fully disassembled, thoroughly cleaned, and all wear parts are inspected and replaced. After a final test, the scroll pump is returned with a 12-month Pfeiffer warranty covering all service work performed.
Repair of scroll pumps
Minor repair |
---|
|
Scroll pumps utility film
On our Utility Film Portal,* you will find a range of videos and documents to support the servicing of Pfeiffer products. The portal also offers additional information and tutorial videos covering our pumps and other products.
*Please note: To gain full access to the Utility Film Portal, registration is required.
Services for diaphragm pumps
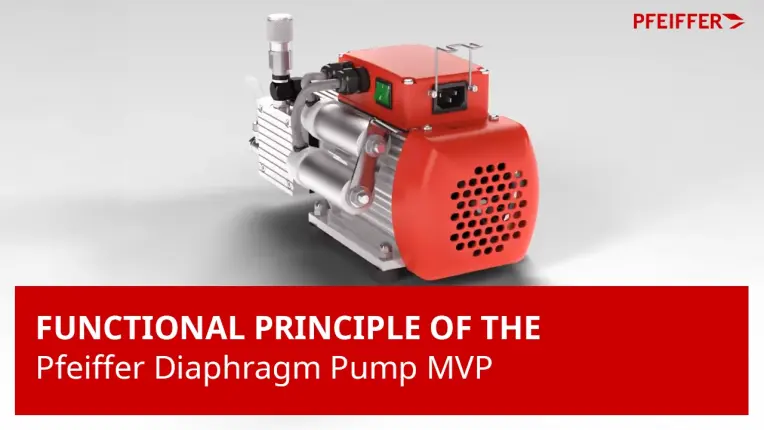
Operational stresses, including mechanical strain and exposure to various gases, further contribute to the degradation of these materials.
Maintenance of diaphragm pumps
Inspection | Maintenance | |
---|---|---|
Optional | Every 2 years1) by operator on site. | Every 2 years1) by Pfeiffer Service. |
|
|
|
Spare parts
|
1) The stated maintenance intervals are only a manufacturer’s recommendation and may vary depending on the application. Possible influencing factors are: stress caused by the application, intensity of use of the product, conditions of the operating environment, non-intended use, incorrect operation.
Repair of diaphragm pumps
Small repair |
---|
|
Diaphragm pumps utility film
On our Utility Film Portal,* you will find a range of videos and documents to support the servicing of Pfeiffer products. The portal also offers additional information and tutorial videos covering our pumps and other products
*Please note: To gain full access to the Utility Film Portal, registration is required.
Services for leak detectors
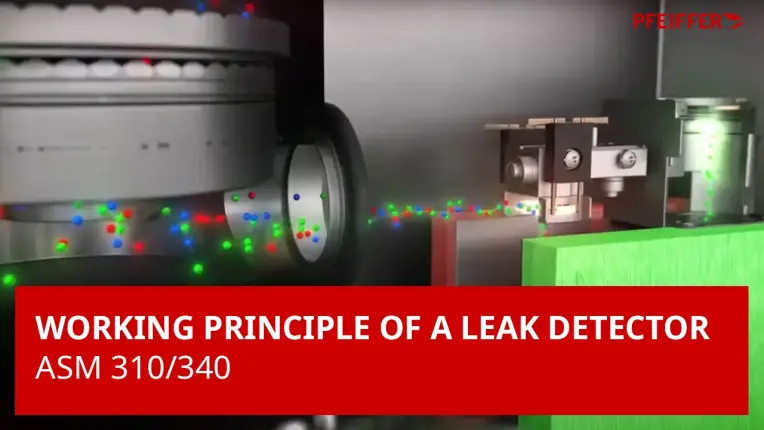
To facilitate maintenance, these systems are equipped with integrated diagnostics that can be accessed during inspections, enabling timely identification and replacement of worn parts.
Maintenance of leak detectors
Regular use
7 hours per day – under clean environment and pumped medium.Essential | Expert | Premium |
---|---|---|
1 year or 2,150 h by Pfeiffer Service.1 | 2 years or 4,300 h by Pfeiffer Service.1 | 4 years or 8,600 h by Pfeiffer Service.1 |
Assessment
| Essential level +
| Expert level +
|
1) The service package will be confirmed upon receipt of your product at our premises.
Intensive use
7 hours per day – under clean environment and pumped medium.Essential | Expert | Premium |
---|---|---|
1 year or 4,300 h by Pfeiffer Service.1 | 2 years or 8,600 h by Pfeiffer Service.1 | 4 years or 17,200 h by Pfeiffer Service.1 |
Assessment
| Essential level +
| Expert level +
|
1) The service package will be confirmed upon receipt of your product at our premises.
Benefits of preventive maintenance
In leak detectors, components such as the operating fluids and seals of the backing pump, as well as the bearings and operating fluids of the turbopump, are subject to wear over time. To monitor their condition, the system includes integrated diagnostics that can be accessed during inspections. Regular monitoring – and, when necessary, replacement – of the internal calibration leak and pirani gauges is recommended to ensure continued measurement accuracy.
Recognizing signs of wear
Early indicators of wear in integrated pumps may include reduced ultimate pressure, elevated operating temperatures, or fluctuating measurement results. Maintenance should be performed as soon as such signs appear to avoid further degradation in performance.
Preventing signs of wear
The diagnostics built into the leak detector support condition-based maintenance, enabling maximum system availability. To maintain optimal performance, it is essential to regularly replace operating fluids, the operating fluid reservoir, and bearings, as well as to check the internal calibration leak.
Repair of leak detectors
- Preventive Premium maintenance as basis
- Depending on the operating hours (regular or intensive use)
- Optional complete overhaul of contaminated detector in our service center
Leak detectors utility film
On our Utility Film Portal,* you will find a range of videos and documents to support the servicing of Pfeiffer products. The portal also offers additional information and tutorial videos covering our pumps and other products
*Please note: To gain full access to the Utility Film Portal, registration is required.